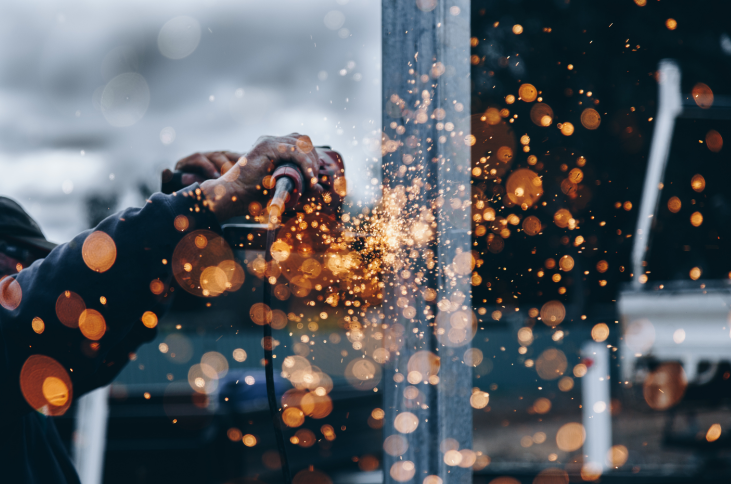
How to Create and Implement an Emergency Preparedness Assessment
By Michael Redmond, Contributor, Continuity Insights
The first step in constructing an effective emergency preparedness plan is to assess current conditions and capabilities, including documenting the organization’s current preparedness assets (for example, describe what the company has available today to address power failures and how it handles them when they occur). A complete inventory of equipment, supplies, and personnel would be included, as would a review of the facilities involved.
Preparing for Industrial Emergencies
Emergency preparedness for an industrial emergency should also involve communications with local emergency managers in the community, such as floodplain oversight agencies, fire and police departments, and environmental agencies. This makes it easier to assess the possible impact of industrial emergencies on the community and to arrange for immediate and cooperative responses on the part of emergency responders.
Having gathered exhaustive information about the facility, staff, and established procedures, the team will then develop a step-by-step outline to describe what must be done to respond to industrial accidents and prevent further damage. These step-by-step outlines should be developed for any conceivable problem (such as flooding, fires and explosions, natural disasters, structural damages, etc.).
The team must ensure that the emergency preparedness plan includes back-ups for major systems that must continue to operate in spite of an industrial emergency. It is important to ensure that alternate power sources are available and that there are alternatives for staffing that will protect health and safety while operations continue. The plan should include steps to protect and retain important company records, and the team should identify any and all training necessary to prepare staff to respond. Finally, the plan should address emergency shut-down and re-start procedures should it become necessary to suspend operations during the industrial emergency.
The team will then present their recommendations to management and most likely to staff as well. After a process of review and revision, the final emergency preparedness plan will be adopted and put in place.
Emergency Preparedness Plan Implementation
After the plan is approved and adopted, it must be put into operation. Facility alterations, equipment configurations and replacements, emergency supply procurements, and a staff training program will be undertaken.
Implementation should include establishing an emergency operations center and a way to ensure communications with state and local agencies that may be involved.
When these efforts are complete, the company should be in a position to address any potential industrial emergency.
Assessing the Effectiveness of a Plan
If an industrial emergency does occur, the team will be responsible for assessing response effectiveness after the fact and then making necessary modifications in the existing plan.
The company should not hesitate to modify current operating procedures to include health and safety measures that become part of the daily routine.
After an industrial emergency, the corporation will have to assess damages and undertake needed repairs and reparations. Depending on the nature of the industry, community involvement and participation may be necessary, and the company should be prepared to work with community leaders and affected citizens who may have been impacted by the emergency. If the emergency preparedness plan has been successful, the company’s prompt, capable response should reassure the community that, despite the potential for industrial emergencies, the industry is an asset to the community.
This article has been republished with permission of Continuity Insights. To learn more about disaster planning and business continuity, visit www.continuityinsights.com.
← News and Insights